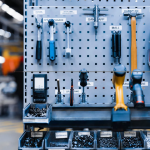
5S es una de las principales herramientas dentro de Toyota Production System y suele formar parte del primer stint en cualquier implantación Lean o TPS. Esto es debido a su fácil comprensión y la rápida visibilidad de sus resultados, aunque más allá de la metodología, su implantación no sea tarea sencilla. Veamos a continuación qué es 5S y su verdadero valor en la implantación de un proyecto lean.
Qué es 5S?
5S no es simplemente una metodología a través de la cual justificar la limpieza y el orden en un espacio de trabajo. Es mucho más que eso.
La mayoría de implantaciones fallidas suelen recaer en una falta de interés por los principios y valores en los que se basa la metodología, y que son los que realmente la hacen especial.
Esta metodología persigue la responsabilidad, la autonomía, el empoderamiento del trabajador en su puesto o área de trabajo, y por tanto, su compromiso para mantenerlo en el mejor estado posible, y su ingenio para encontrar posibles oportunidades de mejora, las cuales permitan realizar las labores de forma más segura, más óptima, más sencilla.
Además, 5S permite iniciar el proceso de sensibilización frente al trabajo estandarizado, ya que exigirá de forma muy sencilla que cumplamos una serie de normas y reglas de fácil cumplimiento. Pero no solo esto, también nos permitirá fomentar la disciplina y rigurosidad en el trabajo, factores clave para el cumplimiento de la calidad o la eficiencia. Pero, ¿en qué consiste esta metodología?
Metodología 5S
5S, como su nombre indica, hacen referencia a 5 palabras japonesas, que resumen el paso a paso que debemos seguir en su aplicación: Seiri, Seiton, Seiso, Seiketsu y Shitsuke.
Estas palabras suelen ser traducidas habitualmente de la siguiente forma:
- Seiri: Separar
- Seito: Ordenar
- Seiso: Limpiar
- Seiketsu: Estandarizar
- Shitsuke: Sostener
5S… ¿Orden y Limpieza?
Es común escuchar – 5S es “orden y limpieza” – aunque, en el mundo occidental, esto es algo ya conocido, y con resultados a la vista lejos del True North. Por eso solemos insistir en las diferencias entre “Orden y Limpieza” y 5S: los puntos críticos para alcanzar el resultado esperado.
Seiri o Separar: Podemos ordenar nuestros bártulos aunque es posible que ninguno de ellos nos sea útil o necesario, por lo que “Orden y limpieza” no cumple ni hace referencia al primer paso de las 5S.
Seiton u Ordenar: la clave está en cómo lo llevemos a cabo. Es de vital importancia discernir qué objetos son de mayor frecuencia de uso, y lograr que exista «un lugar para cada cosa y cada cosa en su lugar». Además debemos aprovechar la gestión visual, y permitir que el puesto de trabajo sea intuitivo, ergonómico y por ende, eficiente. Debemos de evitar esconder los elementos, sino facilitar al máximo el trabajo para lograr la mayor calidad y eficiencia posibles.
Seiso o Limpiar: la importancia de este paso reside en el hábito para detectar los problemas y darles solución. Se dice que la Limpieza es Inspección, pues permite dedicar el tiempo necesario a revisar el estado del elemento. De lo contrario, desconoceremos el verdadero status, y por tanto, nos veremos podremos ver sorprendidos por los problemas.
De forma similar ocurre con Estandarizar (Seiketsu). Es esta fase la que nos permitirá revertir la situación al origen, con la confianza de estar volviendo al lugar de inicio, al mismo orden, al lugar conocido por todos, y no a una nueva situación desconocida para el resto de colaboradores. Es uno de los pasos que más identifica a las 5S, pues su puesta en práctica de la gestión visual permite sin conocimiento previo alguno cumplir uno de los preceptos del Toyota Production System , identificar de forma rápida y sencilla la abnormalidad o situación fuera de estándar.
Finalmente, la 5ª S, Sostener (Shitsuke), no suele estar valorada de forma correcta. Sostener hace referencia al hábito, clave en el desarrollo de la metodología. Sin una revisión periódica y bien definida del estado de nuestras 5S, siempre tenderemos hacia el desorden, y no hacia la sostenibilidad de nuestro puesto o lugar de trabajo.
Pero detrás de todo esto está el cumplimiento de estándares, la disciplina y la rigurosidad, además del trabajo en equipo, el empoderamiento del personal, la libertad para la proposición de ideas y oportunidades de mejora.
Evolución de las 5s a las 6s
Recientemente han surgido otros métodos muy relacionados con el primero como son las 6s que añade la 6ªS de Seguridad al proceso, y que se han desarrollado para la adaptación de la metodología en ciertos ámbitos u organizaciones, pero que no obedece a la definición original del método.
Fuente: Toyota Material Handling.