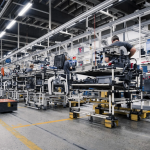
Cuando hablamos de Toyota Production System, implícitamente hablamos de balancear el trabajo y lograr un ritmo productivo lo más fluido posible. Para ello es necesario organizar el trabajo en cada proceso de forma fluida, paso a paso. Hablando claro, significa diseñar plantas en las que el trabajo fluya sin detenimiento directamente de un proceso a otro, sin ningún desvío al almacén. Significa también definir los procesos logísticos de forma que el trabajo se mueva de forma fluida y en tiempo a través de talleres de materia prima, mecanizado y montaje, y a través de nuestros proveedores, concesionarios y clientes.
Continuous Flow: Producción pieza a pieza
Idealmente, los elementos deben avanzar por la secuencia de producción de uno en uno. Esta es la forma más rápida de transformar materias primas en productos terminados. Con ello logramos minimizar la cantidad de WIP o material en proceso en todas las tapas de la producción y alineamos nuestra fabricación con la demanda real del cliente.
La producción en lote unitario no es efectiva, sin embargo, en trabajos donde cambiamos moldes, utillajes, u otras herramientas para producir diferentes productos, como en el forjado, la fundición, la estampación, o el moldeo podría llegar a ser una opción. En este tipo de trabajos, aun así, debemos diseñar procesos de forma que emulen la producción en flujo continuo.
Pasos hacia una producción en flujo continuo
Utilización de lotes más pequeños
Un primer paso hacia la producción en flujo continuo en el procesado de lotes es usar los lotes más pequeños posibles. Teniendo en cuenta que el cambio de moldes o utillajes es un trabajo que conlleva mucho tiempo, tradicionalmente se ha favorecido la fabricación de grandes lotes, con ánimo de aprovechar mejor la capacidad productiva y evitar máquinas paradas.
Sin embargo, grandes lotes suponen grandes inventarios, una de los principales Muda dentro del Toyota Production System. Gracias a lotes más pequeños podemos reducir el inventario y aumentar significativamente la flexibilidad de nuestra organización. Un ejemplo:
Si necesitamos 1000 unidades de un producto A y 1000 de un producto B, podríamos producirlas en 4 lotes de 500 en vez de hacerlo en 2 lotes de 1000. Para hacerlo sin comprometer la eficiencia, debemos encontrar formas que acorten los cambios de utillajes, moldes, etc. Esto es, debemos asegurar que un número mayor de tiradas de producción no aumenta significativamente el tiempo que las máquinas estén paradas.
Herramienta SMED
Históricamente, los avances en la reducción de los tiempos de cambios han sido un importante dinamizador en Toyota Production System. Estos avances son fácilmente alcanzables una vez que los trabajadores reconocen la importancia de acelerar los cambios y reducir los lotes. El truco está en analizar los trabajos para el cambio de forma sistemática. Una buena herramienta para ello es SMED.
Flujo continuo vs Producción por lotes
En la figura más abajo, los trabajadores A, B y C llevan a cabo su trabajo de forma sucesiva en la secuencia de montaje. El trabajo comienza para cada trabajador con una caja de 1000 sub-ensambles que vienen del proceso anterior. Cada uno de ellos ejecuta su trabajo sobre los 1000 sub-ensambles, que luego pasan al siguiente trabajador.
Podemos evitar estos problemas situando a los trabajadores más cerca unos de otros en un flujo continuo, o flujo pieza a pieza, y buscando que cada uno de ellos maneje solo un montaje en cada ciclo. Ejecutarán su trabajo en un único producto y entonces, lo pasarán al siguiente trabajador, antes de tomar un nuevo producto para continuar el trabajo.
PROCESOS SEPARADOS | FLUJO CONTINUO |
![]() |
![]() |
Este approach implica una serie de ineficiencias:
|
Este cambio genera los siguientes beneficios:
|
Impacto en el Lead Time
Echemos un rápido vistazo a la diferencia de Lead Time entre un modelo y otro basado en el ejemplo indicado:
PRODUCCIÓN POR LOTES | FLUJO CONTINUO |
![]() |
![]() |
El ejemplo tiene 3 procesos consecutivos, en el que cada cual requiere un segundo para completar 1 ciclo de trabajo. El modelo de producción en lotes conlleva un Lead time de 3000 segundos. Eso se debe a que las piezas están paradas entre procesos mientras se está llevando a cabo el trabajo en lotes. En el modelo de flujo continuo, seremos capaces de completar 1000 piezas en 1002 segundos, tiempo suficiente para procesar las 1000 piezas de una en una, a través de los 3 procesos.
Flujo continuo, takt time y demanda del cliente
Este concepto no se puede entender de forma independiente al resto de herramientas dentro de Toyota Production System. En especial, es imposible separar esta metodología de trabajo del concepto de Takt time, a través del cual buscamos alinear nuestro ritmo productivo con el de la demanda del cliente final.
La demanda final del cliente es una de las claves del Lean manufacturing, pues nos asegura fabricar únicamente aquello que el mercado demanda realmente y no caer en la sobreproducción, que inflexibilizaría la organización y crearía muchos otros Mudas.
Fuente: Toyota Material Handling.